How to Soldering SMD Power Inductors?
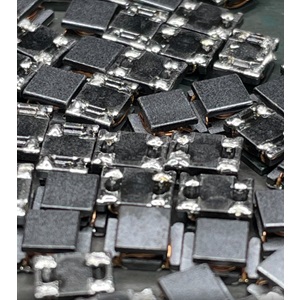
What is a Power Inductor?
A power inductor is an electromagnetic component used to store energy, usually made of enameled copper wire wound on a magnetic core. In electronic circuits, power inductors can be used for filtering, voltage stabilization, current limiting, etc.
How to Soldering SMD Power Inductors?
Soldering of power inductors involves melting and coating the solder on the terminals of the power inductor to form a strong electrical connection.
When soldering power inductors, you need to pay attention to the following points:
Choose the right solder. The melting point of the solder should be lower than the heat-resistant temperature of the power inductor. Commonly used solders include tin-lead solder and lead-free solder. Tin-lead solder has a lower melting point and better soldering properties, but it contains lead and is harmful to the environment and the human body. Lead-free solder has a higher melting point and poor solderability but is relatively harmless to the environment and the human body.
Prepare soldering tools. Soldering tools include soldering iron, solder wire, solder paste, flux, etc. The power of the soldering iron should be appropriate, generally 25W-60W. The diameter of the solder wire should match the size of the soldering iron tip. Solder paste can improve the fluidity of solder, and flux can remove oxides on the solder surface and improve solderability.
Clean the inductor terminals. The terminal surface of the power inductor may be oxidized, affecting the solderability. You can use sandpaper or alcohol to wipe the terminal surface to remove oxides.
Perform soldering. Heat the soldering iron to the appropriate temperature, dip the solder wire, and apply solder to the terminals of the power inductor. The solder should evenly cover the surface of the terminal to form a smooth solder joint.
Cool the solder joint. After the solder melts, you need to wait for it to cool and solidify. Cold air or natural cooling can be used.
- Heat the soldering iron to the appropriate temperature.
- Dip the tin wire and apply a layer of solder on the solder paste.
- Place the soldering iron tip on the terminal of the power inductor and heat the terminal.
- When the temperature of the terminal rises, bring the solder wire close to the terminal, and the solder will melt and flow to the terminal.
- Remove the soldering iron and wait for the solder joint to cool and solidify.
- The temperature of the soldering iron should not be too high, otherwise the power inductor may be damaged.
- The amount of solder should not be too much, otherwise, it may cause solder joints to be soldered or short-circuited.
- After soldering, check whether the solder joint is firm and repair it if necessary.
- Insufficient Solder(IS): The solder joints are not firm and can fall off easily. The reason may be that the soldering iron temperature is too low, the amount of solder is insufficient, or the terminals are not clean.
- Solder Short(SS): Two or more solder joints are connected, causing a short circuit. The cause may be too much solder or uneven soldering.
- Cold Solder(CS): The surface of the solder spot is not smooth and granular. The reason may be that the soldering iron temperature is too low or the solder is oxidized.
Because of the above characteristics, DETZO has developed the FCW-3007S fully automatic inductor soldering machine. High-precision displacement and fast output speed can increase output and save manpower. Welcome to contact us.